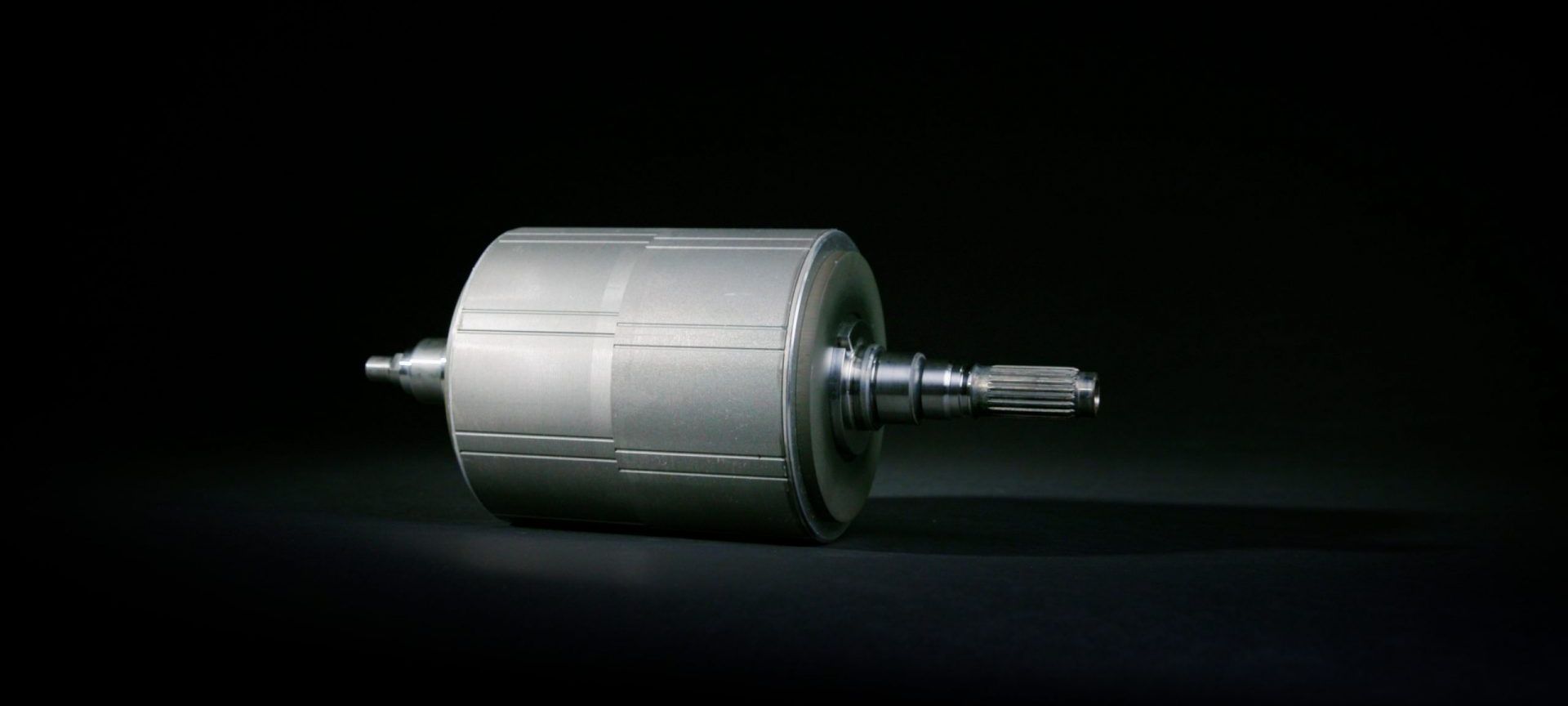
To może być przełom w recyklingu części silników elektrycznych!
Nissan oraz uniwersytet w Wasedzie ogłosiły rozpoczęcie testów wspólnie opracowanego procesu recyklingu elementów silników pochodzących z samochodów elektrycznych. Czy najgorsza bolączka elektryków może się skończyć?
Nissan oraz uniwersytet w Wasedzie ogłosiły rozpoczęcie testów wspólnie opracowanego procesu recyklingu, który pozwala na odzyskiwanie związków metali ziem rzadkich z magnesów stosowanych w silnikach zelektryfikowanych samochodów. To bardzo istotne dla rozwoju elektromobilności, ponieważ o ile pojazdy elektryczne same nie emitują żadnych szkodliwych substancji, o tyle ich budowa o wiele bardziej obciąża środowisko, niż ma to miejsce w przypadku aut spalinowych. Nowe metody recyklingu mają pozwolić na ograniczenie szkodliwych dla środowiska procesów stosowanych w górnictwie i rafinacji, a także pomóc w ustabilizowaniu rynku metali ziem rzadkich. Nissan ma nadzieję, że obecnie prowadzone testy, pozwolą na wdrożenie nowych procesów odzyskiwania tych metali najpóźniej w połowie obecnej dekady.
Recykling pierwiastków z magnesów w silnikach elektrycznych
Większość silników w zelektryfikowanych samochodach wykorzystuje magnesy neodymowe, które zawierają trudno dostępne metale ziem rzadkich, takie jak neodym czy dysproz. Zmniejszenie wykorzystania tych metali jest ważne nie tylko ze względu na ograniczenie szkodliwych dla środowiska procesów stosowanych w górnictwie i rafinacji, ale również na brak równowagi między podażą a popytem, który prowadzi do fluktuacji cen zarówno dla producentów, jak i konsumentów.
Od 2010 roku Nissan już w fazie projektowej stara się ograniczyć zawartość ciężkich pierwiastków ziem rzadkich (ang. REE) w magnesach wykorzystywanych w jednostkach napędowych. Ponownie przetwarza te pierwiastki usuwając magnesy z silników, które nie spełniają standardów produkcyjnych i nie mogą być ponownie instalowane w pojazdach, a następnie zwraca magnesy ich dostawcom. Aktualnie proces ten składa się z kilku etapów, w tym ręcznego demontażu i usuwania komponentów. Stworzenie prostszego i bardziej ekonomicznego procesu jest istotne dla osiągnięcia wyższego współczynnika recyklingu w przyszłości.
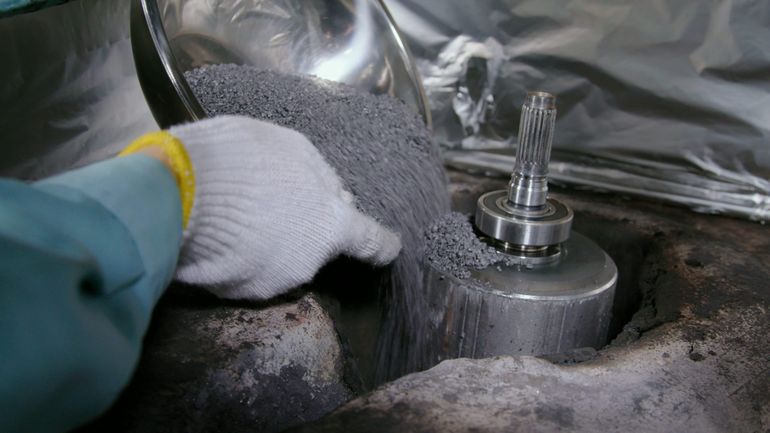
Recykling a samochody elektryczne – jak to się odbywa?
Od 2017 roku Nissan współpracuje z Uniwersytetem w Wasedzie, który ma bogate doświadczenie w badaniu recyklingu i wytapianiu metali nieżelaznych. W marcu 2020 roku udało się w ramach współpracy opracować proces pirometalurgiczny niewymagający demontażu silnika.
Etapy procesu:
1. Materiał do nawęglania i surówka hutnicza są dodawane do silnika, który potem jest podgrzewany do temperatury co najmniej 1400 stopni Celsjusza i zaczyna się topić.
2. W celu oksydacji pierwiastków ziem rzadkich do stopionej mieszanki dodawany jest tlenek żelaza.
3. Do mieszanki dodawana jest niewielka ilość topnika na bazie boranu, który jest w stanie rozpuszczać tlenki pierwiastków ziem rzadkich w niskich temperaturach i ma wysoką skuteczność w ich odzyskiwaniu.
4. Stopiona mieszanka dzieli się na dwie warstwy płynne – jedna z nich to stopiona warstwa tlenków (żużel), która zawiera pierwiastki ziem rzadkich unoszące się na górze, a druga warstwa to stop żelaza i węgla (Fe-C) o większej gęstości, który opada na dno.
5. Pierwiastki ziem rzadkich są odzyskiwane z żużlu.
Testy wykazały, że proces ten pozwala na odzyskanie z silników nawet 98% pierwiastków ziem rzadkich. Przekłada się to także na oszczędność czasu o około 50% w porównaniu do obecnie stosowanej metody, ponieważ nie ma potrzeby rozmagnesowywania, usuwania ani demontażu magnesów.
Najnowsze
-
Test Peugeot 408 GT: masaż na trasie i pazury na ulicy
Niektórzy nazwą go SUV-em w stylistyce coupe, inni fastbackiem, a jeszcze inni powiedzą, że kojarzy im się “z nie wiadomo czym”. Nie można odmówić mu natomiast jednego – Peugeot 408 to bezsprzecznie piękne auto, a wciąż nietypowa na rynku mieszanka kilku rodzajów nadwozia dodaje mu dużego uroku i wyróżnia na ulicach. Bo powiedzmy sobie szczerze – […] -
Test Ford Bronco Badlands – powrót legendy na bezdroża
-
Mercedes Vision V: gdzie podziała się motoryzacja, a pojawił się… 65-calowy telewizor?
-
Do końca wakacji paliwo będzie tańsze? Eksperci ostrzegają: jesienią czeka nas podwyżka, zwłaszcza ON
-
Car of the Year Polska 2026: rekordowa liczba chińskich aut w konkursie. Pełna lista nominowanych
Zostaw komentarz: