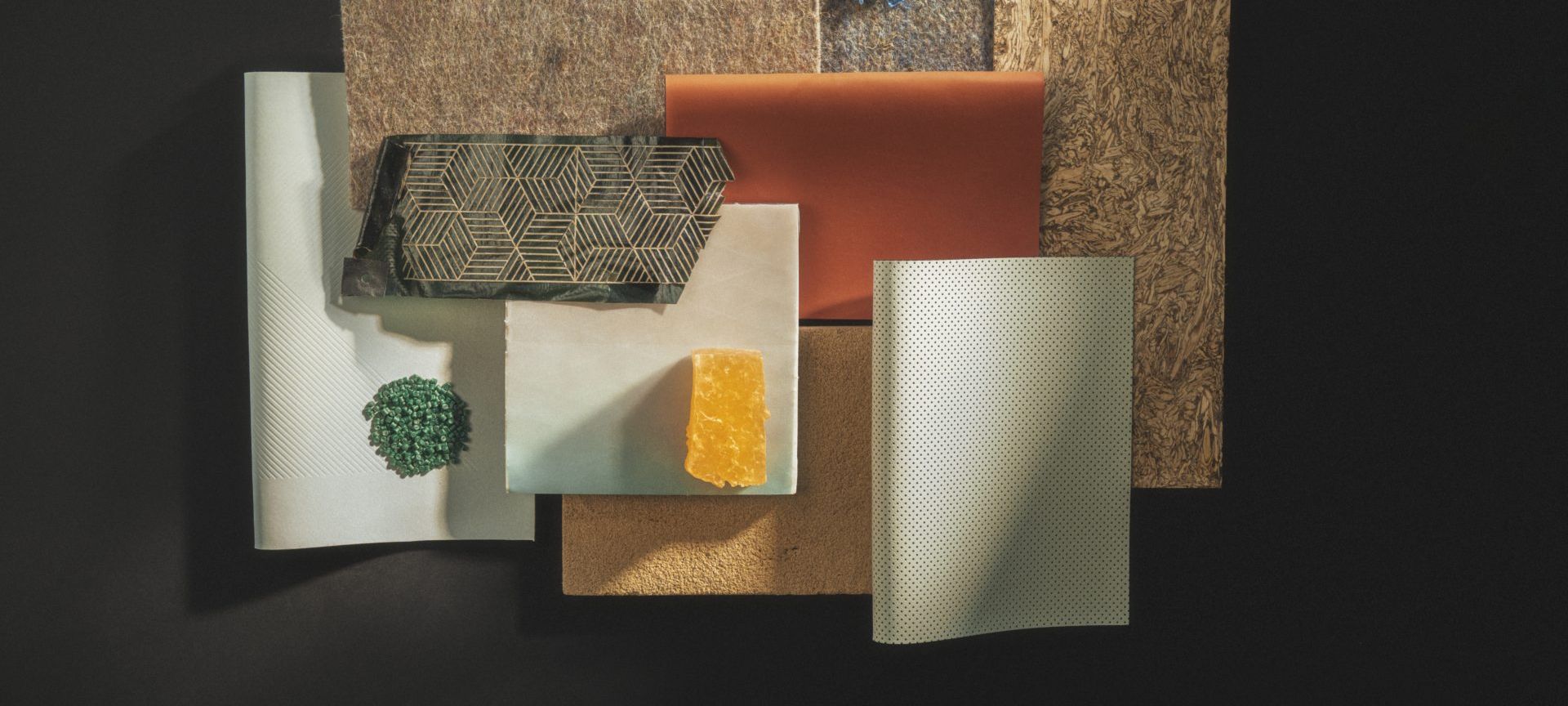
Rewolucja w przemyśle samochodowym: dowiedz się, z czego BMW wyprodukuje części już w 2023 roku
Od 2025 roku nowe modele BMW będą po raz pierwszy wyposażone w elementy wykończeniowe wykonane z tworzywa sztucznego, którego około 30 procent surowca stanowić będą materiały z odzysku. Jakiego?
Spis treści
- Sieci rybackie jako części samochodowe
- Przetwarzanie tworzyw pochodzenia morskiego
- Wegańskie materiały w BMW
- Mirum i Deserttex – nowe materiały zastąpią skóry
BMW Group pracuje nad różnymi metodami wykorzystania odpadów plastikowych z przemysłu morskiego jako surowca do produkcji komponentów samochodowych w celu ochrony cennych zasobów i zmniejszenia emisji CO2. Taka forma recyklingu ma zmniejszać zapotrzebowanie na ropopochodne tworzywa pierwotne, a jednocześnie przeciwdziałać zanieczyszczeniu oceanów. Części będą wytwarzane np. z sieci i lin rybackich pochodzących z recyklingu. Surowiec ten jest prewencyjnie pozyskiwany z portów na całym świecie, aby zapobiec ich wyrzucaniu jako odpadów do morza.
Sieci rybackie jako części samochodowe
Odpady z przemysłu morskiego będą przetwarzane w procesie recyklingu na elementy wykończeniowe, które mogą być stosowane zarówno na zewnątrz, jak i wewnątrz przyszłych samochodów. Powstałe w ten sposób komponenty mają o około 25 procent niższy ślad węglowy niż odpowiadające im komponenty z konwencjonalnie produkowanych tworzyw sztucznych.
Recyklingowane odpady nylonowe to podstawa przędzy z tworzywa sztucznego, z której wykonana jest między innymi wykładzina podłogowa w BMW iX i nowym BMW X1. Materiałem wyjściowym dla Econylu są wysłużone sieci rybackie, a także zużyte wykładziny podłogowe i odpady z produkcji tworzyw sztucznych.
Przetwarzanie tworzyw pochodzenia morskiego
BMW, dzięki nowej inicjatywie opracowanej we współpracy z duńską firmą PLASTIX, chce w przyszłości pójść o krok dalej w recyklingu morskich odpadów plastikowych. Po rozdzieleniu według rodzaju, sieci rybackie i liny będą przetwarzane w innowacyjnym procesie – powstanie z nich plastikowy granulat. Przetworzone tworzywo sztuczne pochodzenia morskiego było do tej pory stosowane jedynie w przemyśle motoryzacyjnym w postaci włókien do nowych elementów pojazdów, a ten recyklat może być po raz pierwszy wykorzystany w formowaniu wtryskowym. Surowiec do produkowanych w ten sposób elementów może składać się w około 30 procentach z morskich odpadów plastikowych.
Stwarza to dodatkowe możliwości zastosowania tworzyw z recyklingu. BMW postawiło sobie za cel zwiększenie do roku 2030 udziału materiałów wtórnych w tworzywach termoplastycznych stosowanych w nowych pojazdach z obecnych około 20 procent do średnio 40 procent.
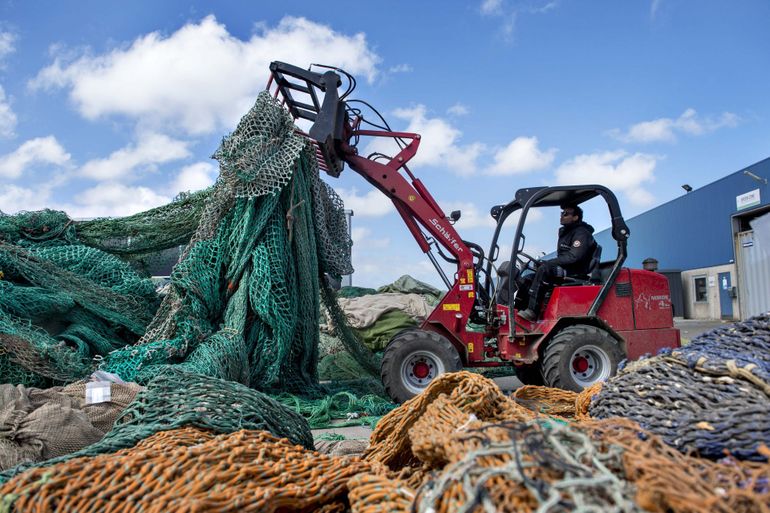
Wegańskie materiały w BMW
Tymczasem już za rok BMW wprowadzi na rynek pierwsze pojazdy z całkowicie wegańskim wnętrzem. Jest to możliwe przede wszystkim dzięki opracowaniu materiałów o właściwościach zbliżonych do skóry. W przyszłości mogą one być stosowane również na powierzchniach kierownic, gdzie muszą spełniać wysokie wymagania w zakresie cech dotykowych, wyglądu premium i odporności na zużycie. W pełni wegańskie warianty wnętrza będą dostępne w modelach BMW i MINI po raz pierwszy w 2023 roku. W ten sposób bawarski producent wychodzi naprzeciw zapotrzebowaniu na wegańskie i nieskórzane wykończenia, które w najbliższej przyszłości jeszcze wzrośnie, szczególnie w USA, Chinach i Europie.
Wraz z wprowadzeniem nowej jakości powierzchni kierownic, odsetek elementów pojazdów noszących ślady materiałów pochodzenia zwierzęcego w pojazdach BMW i MINI spadnie do mniej niż jednego procenta. Oznacza to, że tylko w niewidocznych miejscach pozostają np. różne substancje woskowe, takie jak żelatyna jako składnik powłok ochronnych, lanolina w lakierach, łój jako dodatek do elastomerów i wosk pszczeli jako topnik do lakieru.
BMW od dawna oferuje alternatywę dla skóry w postaci różnych wariantów tkanin. Teraz po raz pierwszy możliwe jest zastosowanie adekwatnego zamiennika skóry na najważniejszym łączniku pomiędzy kierowcą i pojazdem.
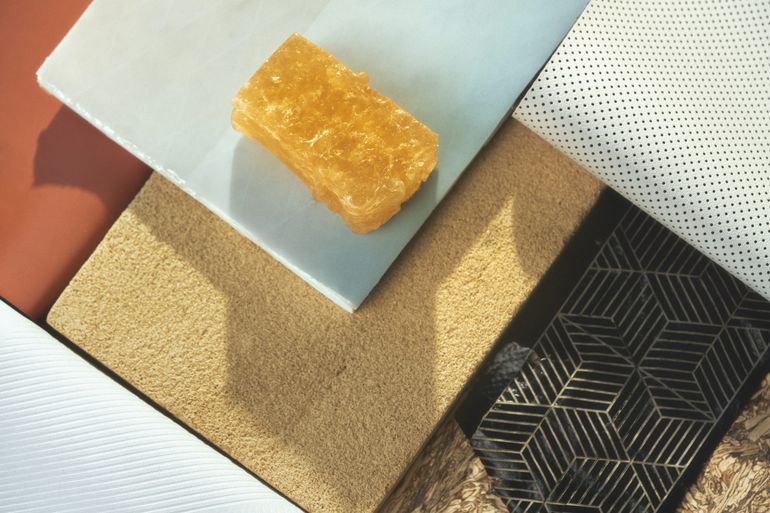
Mirum i Deserttex – nowe materiały zastąpią skóry
W drodze do osiągnięcia neutralności klimatycznej BMW stawia na wykorzystanie energii elektrycznej w produkcji i w łańcuchu dostaw, zwiększa udział materiałów wtórnych i surowców naturalnych, stawia na wydajne silniki elektryczne i spalinowe, a w produkcji – wysoki wskaźnik recyklingu w rozumieniu gospodarki o obiegu zamkniętym.
Przykładowo dywaniki w wielu modelach wykonane są z tzw. monomateriału. W ten sposób eliminuje się mieszanki materiałów, które trudno poddają się recyklingowi. BMW chwali się, że w efekcie oszczędza około 23 tysięcy ton CO2 rocznie i dodatkowo 1600 ton odpadów, ponieważ przetworzone dywaniki i ścinki materiałów są ponownie wykorzystywane w procesie produkcyjnym.
W 100 procentach biopochodny i wolny od ropy naftowej materiał Mirum ma potencjał, aby w przyszłości imitować wszystkie tradycyjne właściwości skóry. Również nowy materiał Deserttex składa się ze sproszkowanych włókien kaktusa i biopochodnej matrycy poliuretanowej.
Obniżenie emisji CO2 w całym cyklu życia pojazdu jest głównym celem BMW Group na drodze do neutralności klimatycznej, która ma zostać osiągnięta najpóźniej do 2050 roku.
Najnowsze
-
Płatne parkowanie a wzrost wypadków motocyklowych – to szokujące dane! Jak jeździć bezpieczniej?
Wydaje się, że przesiadka na jednoślad w mieście to same korzyści - dowiedz się, czy ma to sens i czy jesteś na to gotowy. -
Test BMW 120 – z potencjałem na przyjaciela
-
Nowy Volkswagen Touareg R – flagowy SUV z wtyczką i sportowym zacięciem
-
Foteliki samochodowe na każdą kieszeń: jak znaleźć bezpieczny model w dobrej cenie?
-
Parking w Warszawie: bezkarność na „kopertach” uderza w najsłabszych – kto na tym zarabia? Cena kopert i fałszywych kart
Zostaw komentarz: