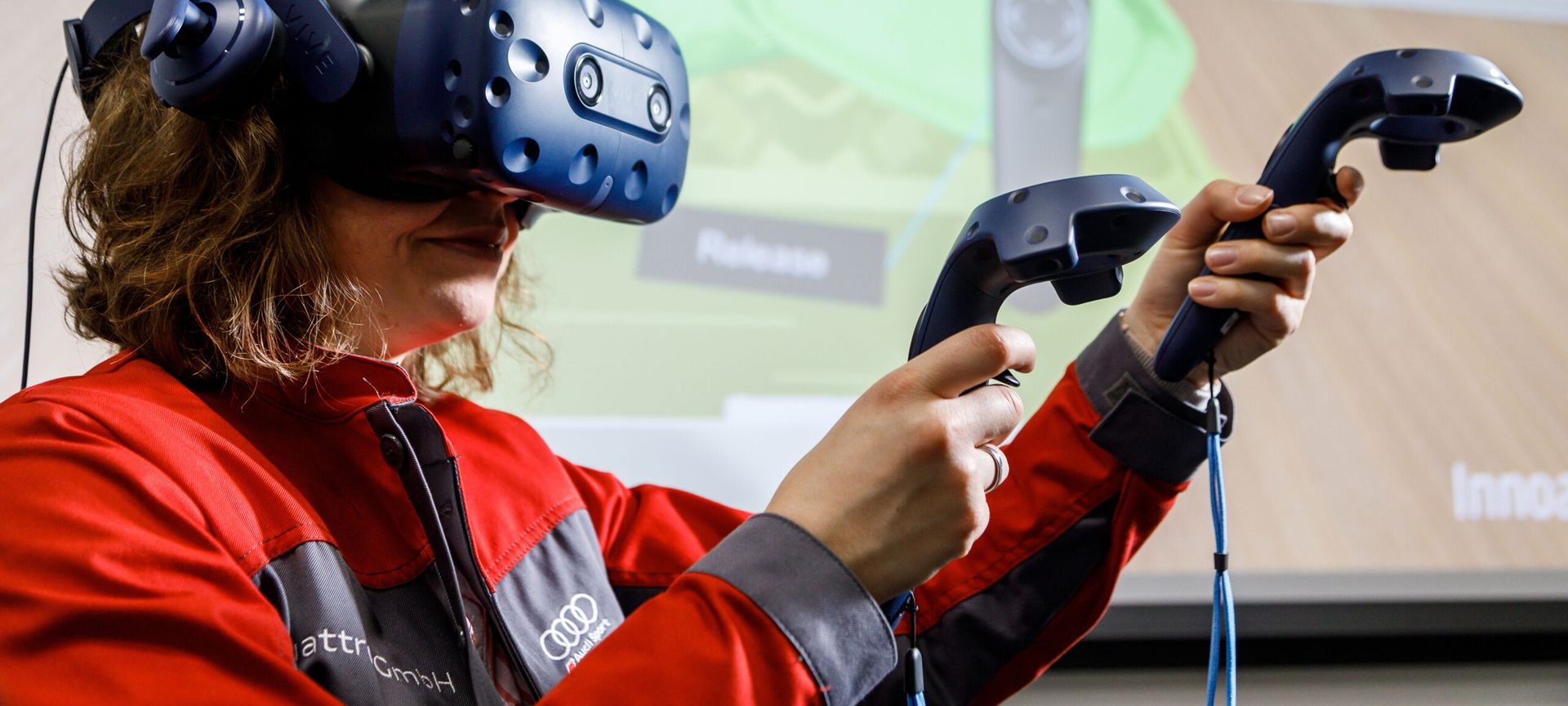
Audi e-tron GT – pierwszy samochód marki, którego produkcja została zaplanowana cyfrowo
Audi e-tron GT to pierwszy model spod znaku czterech pierścieni, którego produkcja została w całości zaplanowana bez używania fizycznych prototypów.
Było to możliwe dzięki wielu innowacyjnym rozwiązaniom technicznym, m.in. dzięki trójwymiarowemu skanowaniu budynków, procesowi uczenia się maszyn (tzw. machine learning) i dzięki wykorzystaniu wirtualnej rzeczywistości. Wszystkie procesy montażowe: procedury i poszczególne czynności wykonywane przez pracowników, zostały przetestowane i zoptymalizowane w przestrzeniach wirtualnych, które w najdrobniejszych szczegółach odwzorowują ich rzeczywiste odpowiedniki.
Planowanie wirtualne jest obecnie stosowane również poza obszarem określonych obiektów, pozwalając na cyfrową, zdalną pracę bez konieczności odbywania podróży służbowych i zleceń zagranicznych. Rozwiązanie to funkcjonować będzie również po zakończeniu obostrzeń związanych z pandemią. Skany 3D i planowanie w przestrzeni wirtualnej sprawiają, że procesy są bardziej wydajne i trwałe.
Gdzie wykorzystywane jest wirtualne planowanie i dlaczego trójwymiarowe skanowanie jest tak ważne w tym procesie?
W konwencjonalnym procesie planowania produkcji każdego nowego modelu Audi wykorzystywane są różne prototypy. We wczesnej fazie planowania wytwarzane są prototypy pojazdów, które są raczej jednorazowymi modelami i w których wiele części wykonanych jest ręcznie. To czasochłonne i kosztowne. Pracownicy planowania montażu wykorzystują te prototypy do definiowania i optymalizacji późniejszych procesów produkcyjnych. Jakie są zadania pracownika? Gdzie musi znajdować się dana część, aby pracownik miał do niej optymalny dostęp? Czy pracownik może samodzielnie trzymać i instalować część? Jak musi się przy tym poruszać? Czy inne części stoją na przeszkodzie? Jakich narzędzi potrzebuje? Podczas planowania produkcji modelu Audi e-tron GT tego typu pytania i udzielone na nie odpowiedzi zostały w całości przeniesione do świata wirtualnego. Każdy krok i każde działanie były testowane w przestrzeni cyfrowej, przy użyciu wirtualnej rzeczywistości. Celem wirtualnego planowania jest takie ułożenie poszczególnych czynności i działań, by podczas późniejszej produkcji pojazdu wszystkie procesy były perfekcyjnie zsynchronizowane i aby cykle linii produkcyjnej były płynnie koordynowane. Wymaga to precyzyjnego i skalowalnego modelowania każdego detalu hali produkcyjnej. Do tego stosuje się trójwymiarowe skanowanie. Za pomocą specjalnego sprzętu i oprogramowania tworzy się wirtualną reprodukcję fizycznego obiektu produkcyjnego, w tym wszystkich urządzeń, narzędzi i półek.
Zakład produkcyjny Audi w Böllinger Höfe, będący częścią fabryki w Neckarsulm, gdzie produkowane jest Audi e-tron GT, również został odtworzony w cyfrowym świecie. A dzięki nowym, cyfrowym metodom planowania, na bazie tego modelu można zaplanować produkcję z praktycznie rocznym wyprzedzeniem.
Jak działa trójwymiarowe skanowanie i jaką rolę w tym procesie odgrywa sztuczna inteligencja?
Urządzenie skanujące ma około dwóch metrów wysokości i cztery koła, dzięki czemu pracownik może przemieszczać je po całej przestrzeni. Na górze znajduje się urządzenie LiDAR (ang. Light Detection and Ranging), trzy dodatkowe skanery laserowe i kamera. Podczas skanowania przestrzeni prowadzone są jednocześnie dwa procesy: kamera szerokokątna robi zdjęcie przestrzeni, podczas gdy lasery precyzyjnie ją mierzą i generują trójwymiarową chmurę punktów otoczenia. Tylko w zakładach w Neckarsulm zostało już zeskanowanych przy użyciu tej techniki 250 000 metrów kwadratowych powierzchni hal produkcyjnych. To, że generowane punkty, obrazy i zbiory danych stają się użytecznym obrazem ogólnym, który może być wykorzystany w istniejących systemach planowania, wynika z interakcji pomiędzy sprzętem a oprogramowaniem. Zastosowane tu oprogramowanie jest własnym opracowaniem Audi, opartym na sztucznej inteligencji i zasadzie uczenia się maszyn (ang. machine learning). Chmura punktów i zdjęcia są łączone w trójwymiarową, realistyczną przestrzeń podobną do tej, którą widać w Google Street View. Proporcje i rozmiary są prawdziwe, odpowiadają rzeczywistości, ale można je skalować. Oprogramowanie automatycznie rozpoznaje wszystkie obiekty w przestrzeni.
Skaner za każdym razem uczy się też jeszcze dokładniej automatycznie rozpoznawać, rozróżniać i klasyfikować obiekty. Na przykład: system odróżnia półkę od stalowej belki konstrukcji hali. Pozycja półki może być później zmieniona w programie i w przestrzeni wirtualnej, a pozycja stalowej belki nie. Dane te umożliwiają wirtualne przejście przez zeskanowany zakład produkcyjny z dowolnego punktu początkowego i mogą być bezpośrednio wykorzystane w procesach planowania.
Gdzie jest już wykorzystywane planowanie w wirtualnej rzeczywistości i jakie korzyści przynosi?
Audi e-tron GT jest pierwszym modelem z czterema pierścieniami w logo, którego procedury produkcyjne i związane z nimi procesy logistyczne zostały przetestowane wyłącznie wirtualnie, bez żadnych fizycznych prototypów.
W związku z tym przygotowywano kompleksowy, wirtualny, cyfrowy model procesu montażu, w którym uwzględniono dane pojazdu, dostawy materiałów, urządzenia, narzędzia i przebieg następujących po sobie działań i czynności. Jednym z elementów tego modelu są trójwymiarowe skany. Model cyfrowy jest podstawą do dalszych innowacji procesu. Andrés Kohler, odpowiedzialny w Audi za wirtualne planowanie montażu mówi: „Dzięki opracowanemu przez Audi rozwiązaniu VR i cyfrowemu modelowi, koledzy z całego świata mogą się teraz spotykać w przestrzeni wirtualnej i znaleźć się w środku zakładu produkcyjnego jutra. Mogą spoglądać „przez ramię” cyfrowym pracownikom wykonującym zaplanowane procedury. Mogą również w tej aplikacji doświadczyć i zoptymalizować procesy dla dowolnych wariantów produkcyjnych.” Wyniki mogą być następnie wykorzystane do szkolenia pracowników, również w oparciu o aplikację VR. Nowe możliwości są obecnie wykorzystywane w coraz większej liczbie projektów i w wielu miejscach. Na przykład w zakładzie Audi w San José Chiapa w Meksyku odbyły się już warsztaty 3P (3P = Production Preparation Process – proces przygotowania produkcji), w których uczestniczyli również członkowie zespołu projektowego z Ingolstadt. Wcielając się w cyfrowe awatary, a więc całkowicie wirtualnie, eksperci omówili i zaplanowali produkcję Audi Q5 oraz nowego Q5 Sportback.
Wszystkie procedury montażowe, podobnie jak aspekty dotyczące ergonomii, dokładnego rozmieszczenia maszyn, półek i części wzdłuż linii montażowej, są określane i testowane w czasie rzeczywistym. Audi jest w Grupie Volkswagen liderem prac nad rozwojem kompleksowych rozwiązań VR i modeli cyfrowych. Pod kierownictwem specjalistów z Ingolstadt i Neckarsulm, projekt ten jest obecnie wdrażany we wszystkich markach Grupy.
Coś więcej niż tylko budynki i procesy: jak działa wirtualne planowanie transportu podzespołów?
Wirtualne planowanie nie ogranicza się tylko do procesów i procedur pracy. Za pomocą tej technologii można również planować transport i magazynowanie wrażliwych części w specjalnych pojemnikach. Pojemniki te zostały zaprojektowane dla przechowywania i transportowania pojedynczych, szczególnie wrażliwych części Audi e-tron GT, takich jak moduły elektryczne lub części wewnętrzne. W projektowaniu również użyto aplikacji wirtualnej rzeczywistości zamiast wielu fizycznych prototypów z żelaza i stali. Wirtualne planowanie transportu i magazynowania takich pojemników działa następująco: Ponieważ istnieją zestawy cyfrowych danych dla wszystkich części, można je wczytać bezpośrednio do aplikacji VR i w razie potrzeby odpowiednio skalować. Podobnie jak na warsztatach 3P, tu również wielu pracowników z różnych miejsc spotyka się w wirtualnej przestrzeni, ćwicząc najbardziej optymalne i dopasowane do potrzeb warianty transportu i przechowywania takich pojemników z częściami. W proces zaangażowani są również pracownicy działu logistyki, planowania montażu, bezpieczeństwa pracy, zapewnienia jakości, planowania przepływu materiałów oraz dostawcy. Do oznaczania swoich zmian na wirtualnych pojemnikach używają cyfrowych długopisów. W trakcie tego procesu kontenery są ładowane i rozładowywane, przenoszone i mierzone.
Jednym z celów tego planowania jest optymalne bezpieczeństwo części podczas transportu. Ponadto pracownicy lub robot muszą być w stanie łatwo chwycić część i zdjąć ją z pojazdu transportowego. Po zakończeniu wirtualnego ćwiczenia, dane projektowe procesu są eksportowane do większego systemu, a na ich podstawie produkuje się pojazd transportowy.
Co wpływa na to, że wirtualne planowanie jest zrównoważone środowiskowo i ekologiczne?
Czasami mniej oznacza więcej. Stąd płyną trzy wytyczne, czyniące wirtualne planowanie zrównoważonym środowiskowo:
– Mniej zasobów: wirtualne planowanie produkcji Audi e-tron GT bez użycia fizycznych prototypów pozwoliło zaoszczędzić nie tylko czas, ale także materiały, a tym samym zasoby naturalne. To samo odnosi się do projektowania środków transportu oraz magazynowania i transportowania pojemników z częściami. Tworzenie prototypów z żelaza i stali wymaga zasobów i energii, wirtualne planowanie czyni to w wielu przypadkach zbędnym.
– Mniej odpadów: Dotychczas delikatne części były często transportowane w uniwersalnych pojemnikach z niestandardową wykładziną ochronną. Wykładzina ta jest jednak jednorazowego użytku, a zastosowanie nowych, specjalnych i niestandardowych kontenerów sprawia, że jest ona zbędna. Dzięki temu wirtualne planowanie bezpośrednio ogranicza ilość odpadów.
– Mniej podróży służbowych: Zrównoważony rozwój i ochrona środowiska to podstawowy cel koncernu z Ingolstadt. Jednak w czasach pandemii koronawirusa istnieją również powody zdrowotne, by jak najbardziej ograniczyć liczbę podróży służbowych. Wirtualne planowanie wydatnie w tym pomaga. Procesy, które kiedyś wymagały fizycznego spotkania, teraz są możliwe w przestrzeni wirtualnej.
Najnowsze
-
Kambodża na motocyklach: dżungla, świątynie i prawdziwe wyzwania
Oto motocyklowa przygoda w sercu królestwa Kambodży - nie tylko dla twardzieli! Para motocyklistów z Polski przemierza świat i dzieli się z nami wrażeniami. -
Płatne parkowanie a wzrost wypadków motocyklowych – to szokujące dane! Jak jeździć bezpieczniej?
-
Test BMW 120 – z potencjałem na przyjaciela
-
Nowy Volkswagen Touareg R – flagowy SUV z wtyczką i sportowym zacięciem
-
Foteliki samochodowe na każdą kieszeń: jak znaleźć bezpieczny model w dobrej cenie?
Zostaw komentarz: